Day One
- elliemraz
- Apr 30, 2021
- 3 min read
Updated: Jun 4, 2021
My alarm went off at 6:00AM. I got up just like I do on an ordinary school day except when I opened my closet, I had to pause. This was no ordinary day. What do I wear for oyster farming? I pulled on old black running leggings, calf-high Nike elite socks, a long sleeve T-shirt, and an old sweatshirt. I threw on my rain boots and hopped in my Jeep. After a short drive down the beachy Duxbury streets to the harbor, I spotted my new boss, Kevin, already out on the boat in his bright orange Gruden's waders. I joined Kelsey, a talkative young woman with teal blue hair, and we loaded the flat bottom oystering skiff with orange plastic crates in the cool May air. My one month seed to table internship at the Duxbury Oyster Company had begun! We drove the skiff out to the company's float, a small floating dock with what looks like my mom's garden shed perched on top. There, I pulled on my new uniform, a pair of enormous army green waders, buckling the straps over my shoulders. We continued driving the boat out into the bay towards the buoy field where my first job was to lug lines of 6 oyster-filled cages (called holding cars) out of the water one after another and into the boat. I sure was glad to have done so many push ups this spring during track practice. These oysters were from the 2019 crop and had been sitting in these cages for a few months while they finished growing. The cages are tied together with a rope and are attached to a buoy.
We drove back to the float, poured the caged oysters into crates, and placed them in the soaker, part of the float's platform lowered below the water's surface. As the tide rushed out of Duxbury Bay, we drove over to another spot on the company's three acres of land where oyster seed had been dropped in 2019. After receiving instructions from Kevin, I lowered myself into the knee-high water, my waders immediately suctioning to my legs. I grabbed a rake and a stack of orange crates and got to work. The water continued to get lower as the hours passed and the tide went out. Duxbury Bay has up to 11 foot tides, so the difference between high and low tide is very significant. The oystering process is simple as long as you work with the tide: pick a spot and rake the oysters into a pile while the tide finishes going out and then comes back in. It is a race against the tide. Raking and raking, my feet sank deeper into the mud. When I needed to move to a new spot, I had to yank my feet out of the ground. Before I learned the technique of moving your feet as you raked, I yanked at my foot so hard I lost my balance and fell backwards into the two-foot deep 45 degree water. The water rushed into my waders soaking my legs and feet. I laughed along with Kevin and Kelsey saying, "Gotta happen on the first day." The tide continued going out until the water was just to our ankles. The piles of oysters we had been raking emerged. As the tide came back in we scooped the oysters into the orange crates and hoisted them back onto the boat. We headed to shore and made the 10 minute drive to the shop on the other side of town.
The Duxbury Oyster Company's shop is a large garage with a freezer, sorting tables, and an upstairs office. We hauled the crates into the large walk-in freezer then got to work culling (sorting). I poured a crate of unculled oysters onto the table with two other crates on either side of me and two placed below allowing me to cull the oysters into the six designated piles. After an hour, I started to get the hang of it, picking up speed. Kelsey washed the sellable oysters with fresh water, packaged orders, and drove to drop them off in the Duxbury Oyster van. The oysters are packaged in black fishnet bags, with each bag containing 100 oysters. By mid-afternoon I was covered in mud and smelled like the ocean, exactly what I expected. To celebrate my first day, Kevin handed me a bag of oysters to bring home, fresh from our day's harvest.


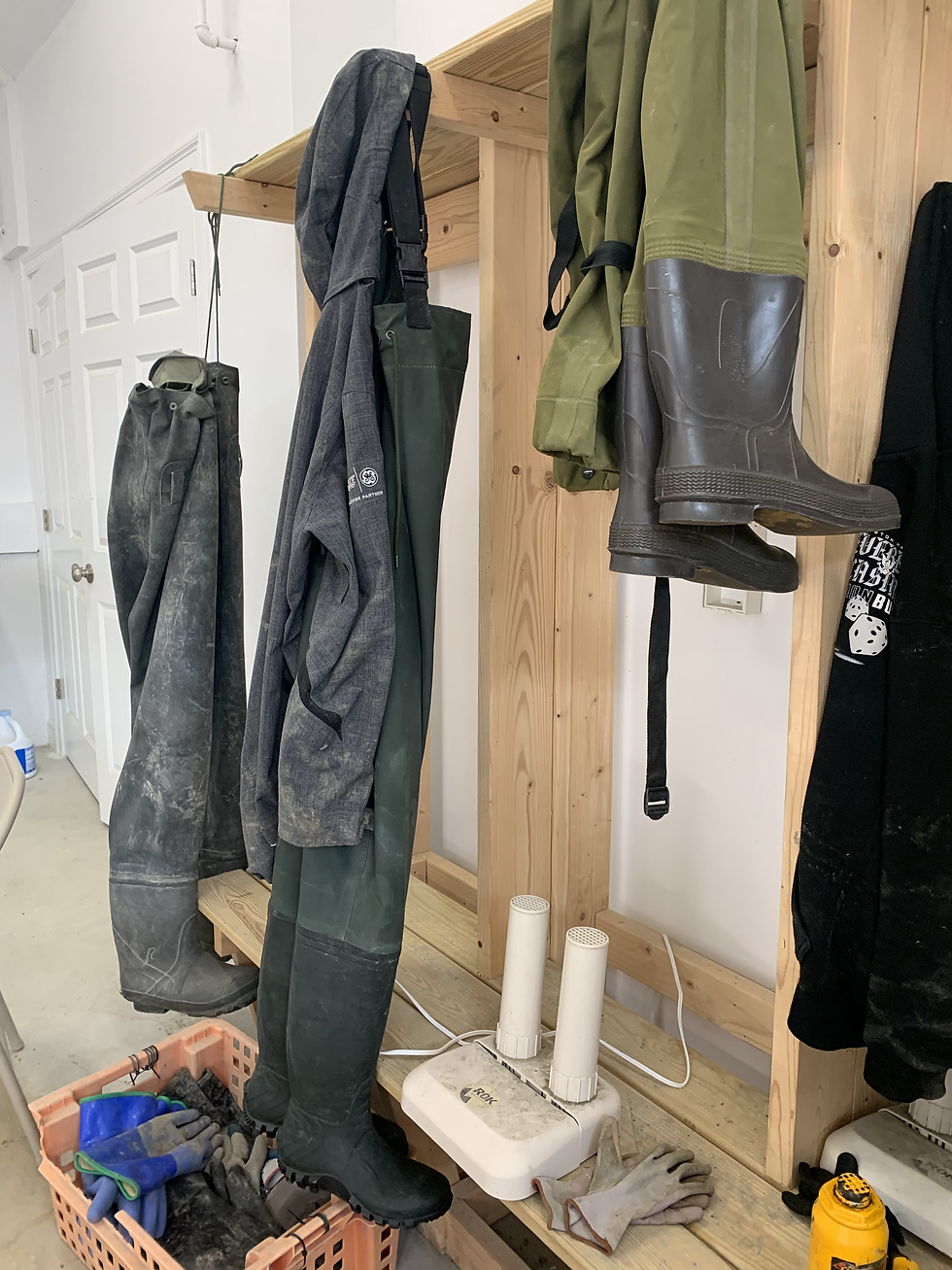
Comments